One of the most common questions about DC electric bow & stern thrusters is how long they can run continuously before overheating, and the answer is dependent on three main factors. In this article, we'll detail what those factors are as they relate specifically to Sleipner (Side-Power) thrusters.
What Triggers the Thruster Motor to Shut Down?
All DC electric motors generate heat as they operate, and at a certain point of continuous operation they will overheat and begin to breakdown. For this reason, all of Sleipner's DC electric thruster motors have thermal-overload protection. In the case of their standard on/off thrusters, which are either on and operating at 100% power or off and dormant, they're protected with a bimetal mechanical "thermoswitch". This type of switch works by using metal which expands when heated, and when the metal expands to a certain point, it triggers a switch which shuts the motor down to protect it from any further heating. Because the metal doesn't always return exactly to its pre-expansion size as it cools down, triggering a mechanical thermoswitch multiple times may cause it to become more sensitive and shut the motor down at lower & lower temperatures.
In the case of Sleipner's proportional-speed thrusters, the thermal overload protection is done with an electronic temperature sensor which is programmed in the system's internal software to shut the thruster down when it reaches a certain temperature. This style of sensor does not become more sensitive over time.
3 Contributing Factors to Overheating & Run Time
1. Voltage & Amperage
Sleipner offers many of their thruster models in either 12-volt or 24-volt power. Because the amperage draw (A) of an electric motor is equal to the wattage (W) of the motor divided by the voltage (V) of the power supply, motors of the same wattage will draw twice as many amps at 12 volts as they would at 24 volts. For example, a 1000W motor draws 83.3A at 12V, but only 41.6A at 24V. The more amperage a motor draws, the quicker it heats up, so a 12V motor will heat up roughly twice as fast as a 24V motor of the same size, and therefore the 12V motor will have about half the continuous run time of the 24V motor.
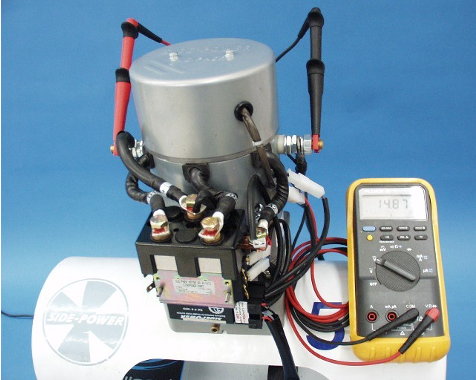
2. Ventilation & Ambient Temperature
The difference in continuous run times between a thruster motor installed in a large, well-ventilated compartment versus one located in a cramped space with little airflow can be quite significant. Ambient temperature matters as well, so your thruster may not run as long on a scorching hot day as it would in cool or mild temperatures. Similarly, a thruster motor located in an engine room may run for longer when you're leaving the dock and the engine hasn't warmed up yet than when you return back to the dock after running the engine for a few hours, heating up the engine room.
Because ventilation is important to extending run times, an ignition-protected (IP) motor will have a shorter run time than the same motor without an IP housing. Sleipner's IP motors are built with a sealed housing which encases the motor to keep gasoline fumes from getting into the motor & solenoid assembly so that the fumes won't ignite due to a spark generated by the thruster motor. Keeping gasoline fumes out also means keeping heat in, so an IP motor will trigger its thermal overload protection faster.
3. On/Off vs. Proportional Speed Thrusters
Similar to the equation relating to volts, watts and amps, a thruster motor that is running at 100% of its power output will heat up much faster than one that is running at less than full power. Because a traditional on/off thruster can only operate at 100% of its power, there is no way to avoid tripping the thermal overload. Sleipner designs the on/off motors to run for roughly three minutes continuously in normal conditions before tripping the thermoswitch. However, Sleipner's proportional speed thrusters allow you to run the thruster at any percentage of its power, essentially giving you a throttle for your thruster, and therefore extending the run time exponentially. Theoretically, the run time of a proportional-speed thruster is infinite when being operated at less than 50% power, and the run time is limited only by how long the batteries can provide power before draining.
How to Increase Run Time of Thrusters
Based on the three main factors that contribute to thrusters overheating and thus shutting down, the easiest way to extend the run time of your thrusters is to purchase and install a proportional speed system. If you already have on/off thrusters installed on your boat, but you're interested in proportional speed, you don't need to purchase a completely new system, as Imtra offers SEP Upgrades to turn your on/off thruster motors into proportional speed thrusters.
If you're happy with your on/off thrusters and just want to extend the run time, consider the other factors. Make sure your battery bank and wiring that power the thruster are properly sized for the model of thruster installed on your boat. Also be sure that the area around your thruster motor is well ventilated and the heat generated by the motor can dissipate.
If you have any questions or would like any additional information relating to Sleipner thrusters don't hesitate to reach out to us, we're here to help!
Further Reading:
5 Common Questions About Proportional Speed Control Bow & Stern Thrusters
5 Tips for Maintaining Your Bow and Stern Thrusters