As with any piece of marine or electrical equipment, anchor windlasses sometimes fail. Luckily, windlass failures are very rarely catastrophic, and the issue can often be diagnosed and repaired simply. This article will go through the common issues that can arise with an anchor windlass, and then how to diagnose and resolve them.
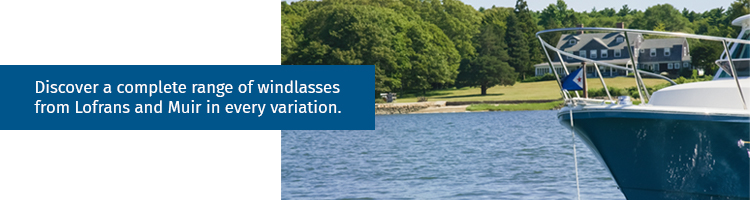
Issue #1: Your Electric Anchor Windlass Won’t Run in Either Direction
If your windlass motor won’t run when it is activated with the control, it means something in the circuit isn’t getting power. That could be the control (dash switch, footswitch, handheld remote, etc.), the solenoid control box, or the windlass motor itself. To determine where the issue is, all you’ll need is a voltmeter.
Steps to try
- It’s generally best to start with the simple solutions first. In all electrical windlass installations there should be a circuit breaker that is designed to trip if the circuit is overloaded to prevent electrical fires. So the first thing to check is if the breaker has tripped. If it’s not immediately obvious from the design of the breaker, simply check voltage on the input side of the breaker, and then the output side. If there’s good voltage on both sides, the breaker is on and functioning.
- Next, take the voltmeter directly to the positive and negative terminals on the windlass motor itself. If no voltage is present, there’s likely a break in one of the battery cables that is supplying power. If the voltage is good, try running the windlass again with your voltmeter still reading the windlass motor. If the voltage drops significantly (less than 9V in a 12V system or less than 19V in a 24V system) then the electrical system is not providing enough power to run the windlass motor. This can be caused by insufficient or drained batteries, battery cables that are too small in diameter, or a loose or broken connection.
- To determine which it is, take the voltmeter to the battery that supplies power to the windlass and run the same voltage test as above: attempt to run the windlass with the voltmeter reading the positive and negative terminals on the battery. If the voltage drops at the battery like it did at the motor, then the issue is with the batteries themselves. Either they are undersized or not sufficiently charged. If the voltage is strong at the battery, but dropping at the motor, then the issue is somewhere in the battery cable. It is either too small in diameter or there is a loose or broken connection. For proper cabling size, refer to the ABYC 10% Voltage Drop table.
- If the voltage is good at the battery and the windlass motor, then the issue is likely in the solenoid control box or the control itself. Most electric windlass installations include a solenoid control box that is between the control switch and the motor. It’s generally installed on a bulkhead in the bow area, near the windlass. Locate the control box and check with the voltmeter that power is passing through the box.
- Activate the control either up or down, and have the voltmeter attached to the corresponding up or down signal wire coming from the control to the control box, which is generally attached to a small spade terminal, not the larger lugs on the control box. If you’re unsure of the wiring, contact the manufacturer or installer for a wiring diagram. If no voltage is present on the signal wire from the control to the control box, then the issue is with the control itself, be it a footswitch, dash switch or handheld remote.
- If there is a signal coming from the control, check the output of the control box next. This is generally the larger lugs on the control box, which hold cables that connect the control box to the windlass motor. Again, test for voltage while trying to run the windlass up or down. If you’ve already determined that the control is outputting a signal to the control box, but the control box is not outputting that same signal to the windlass motor, then the control box has failed and requires replacing.
![Control Box]()
Note: if you hear repeated clicking from the control box when it is activated, that is often an indicator that the contacts inside it have been damaged over time due to running with insufficient voltage. So if this is the case, replacing the control box will only be a temporary fix, and the underlying voltage issues in the battery capacity or cable sizing must also be addressed.
- If the system passes all of these voltage tests, and the windlass motor still will not run, then the issue is internal to the windlass motor and it must be repaired or replaced.
Issue #2: Your Electric Anchor Windlass Will Run in Only One Direction
If the windlass motor is running, but only in one direction, the troubleshooting steps are similar to the steps if it isn’t running at all. The only difference is that you do not need to check voltage at the battery or breaker, as the windlass running in one direction proves that power is present in the circuit. Instead, follow steps 4 through 7 above specifically for the direction that the windlass is not running.
Issue #3: Your Electric Windlass Motor is Running but the Chainwheel Doesn’t Turn
If the windlass motor runs, but the windlass isn’t deploying or retrieving the anchor rode, the most common issue is with the clutch adjustment. Most windlasses have a clutch adjustment, which when loosened allows the chain to freefall. When loose, the clutch allows the chainwheel to spin independent of the main-shaft which is driven by the motor. Therefore, if the clutch is loose, the motor can run and turn the shaft, but the shaft isn’t making contact with the chainwheel to deploy or retrieve the chain.
![Adjusting the clutch]()
Steps to try:
- To tighten the clutch, consult the owner’s manual for your specific windlass. On a vertical windlass, there is typically a star-shaped socket that will accept a winch handle that can be used to tighten or loosen the clutch. Be sure to consult the owner’s manual however, as sometimes these clutch adjustments are left-hand threads that can be broken if they are cranked in the wrong direction. On a horizontal windlass, the clutch adjustment is usually a wingnut or screw at the end of the shaft that can be tightened or loosened.
- If the clutch adjustment is tight, and the motor is still running with no action on the chainwheel, then there is likely a stripped or broken gear internal to the windlass gear box, or broken key and keyways that are causing the motor not to engage with the main-shaft. At that point the windlass should be disassembled and inspected by a marine mechanic or boat yard.
- If you’re trying to deploy your anchor and the motor is running and making a “clunking” or “clicking” noise and the anchor isn’t deploying, it’s likely that the chain or rope is tangled or caught inside the anchor locker. Windlasses are designed to not run when there is resistance on deployment to avoid doing any damage to the deck or anchor locker. Therefore, if there is resistance caused by a tangle or snag in the anchor locker, the windlass will not power-through the resistance. This is a common issue on sailboats that heel over, causing the chain to tumble within the locker. The same is true of boats that just endured rough seas causing the chain pile to fall over itself and become tangled.
Issue #4: Your Electric Windlass Motor Runs, but not at Full Strength
Occasionally after a boat has sat dormant for several months, the windlass labors and lacks the recovery power or speed it had in years past. This can be the result of a number of things. It’s presenting as an electrical issue but, don’t rule out the possibility of a mechanical problem.
Steps to try:
- Begin by checking voltage at the windlass motor. Low voltage can result in damage to the solenoids and will surely slow the speed of the windlass.
- When a windlass motor operates, the armature rotates and the brushes within the motor wear down. Brush wear is a slow process that occurs over seasons of use. Motor brushes can wear to the point where they no longer make the positive contact or they no longer slide smoothly in their carriers. That’s an indication to source a new brush set from your dealer. This brush wear results in a build up of carbon dust inside the body of the motor. Over time, this carbon dust build-up can affect the motor’s performance. High pressure compressed air will help to blow out the carbon dust and may just give that old motor a bit more power and speed. Be sure to wear a mask when blowing out carbon dust, as inhaling it can be dangerous.
- Some windlasses require main-shaft lubrication where they pass through the deck-plate. It’s not uncommon to see a grease fitting (Zerc fitting) at the base of a vertical windlass. Often, a few pumps of grease will lubricate and free up the main-shaft allowing it to rotate with less resistance. White lithium grease is recommended.
- If a windlass seal protecting a main-shaft bearing fails, the bearing can become corroded and eventually seize or fail. Resistance from a failing deck-plate or shaft bearing may slow and labor the windlass. Eventually, the breaker will trip but in the early stages of a failure, the windlass may just seem slower than usual. Consult your dealer for replacement bearing and seals. They will often have an exploded parts drawing to assist you in dis-assembly process.
Final Thoughts
These troubleshooting steps cover the most common issues that arise with electric anchor windlasses, but of course they are not exhaustive. There are other less common failures and issues that can arise, and if that is the case be sure to consult an expert.
To avoid common windlass failures, be sure to check out our 7 Tips for Annual Maintenance of Your Anchor Windlass, or feel free to contact us directly to speak with one of our experts.

Related Articles
Related Products: